Роботы и люди. Как производят материнские платы на заводе в Шуе
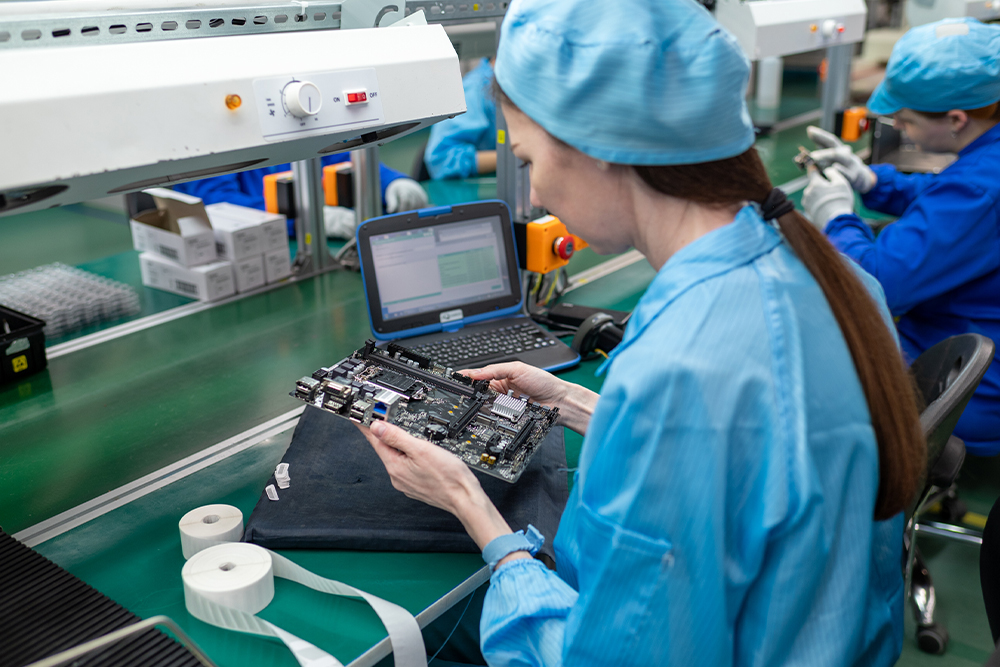
Комплектация и нанесение паяльной пасты
Просторные цеха с высокими потолками и большими окнами скорее напоминают медицинскую лабораторию, чем завод: чисто, светло, аккуратно. Сотрудники одеты в синюю и зеленую форму, похожую на одежду медперсонала. Многие работают в специальных шапочках и перчатках.
Первый цех — комплектация. У каждой детали материнской платы есть свой QR-код. По нему в случае дефектов или поломок можно проследить, из какой партии и от какого поставщика поступила деталь, а также кто и когда работал с ней уже на заводе.
В отделе монтажа печатных плат на пластинки зеленого цвета — «фундаменты» будущих материнских плат — наносят паяльную пасту. Эту технологическую операцию выполняет специальное оборудование: распределяет пасту при помощи трафарета, определяет силу прижатия и скорость движения. «Для каждой платы это индивидуальные параметры, и они на 90% определяют качество дальнейшей сборки изделия», — поясняет Дмитрий Реутов, глава производственно-технологической дирекции «Аквариуса».
Система решает, соответствует ли результат нанесения пасты заданным параметрам и требуется ли корректировка. Изображение образца, на который ориентируется робот, выводится на монитор, установленный над станком, — с его помощью сотрудники завода дают команды роботу.
Сейчас на заводе есть две линии, на которых наносят паяльную пасту. Первую «Аквариус» купил раньше на собственные средства, вторую — на заем, полученный от Фонда развития промышленности (ФРП), что позволило увеличить производительность завода почти вдвое.
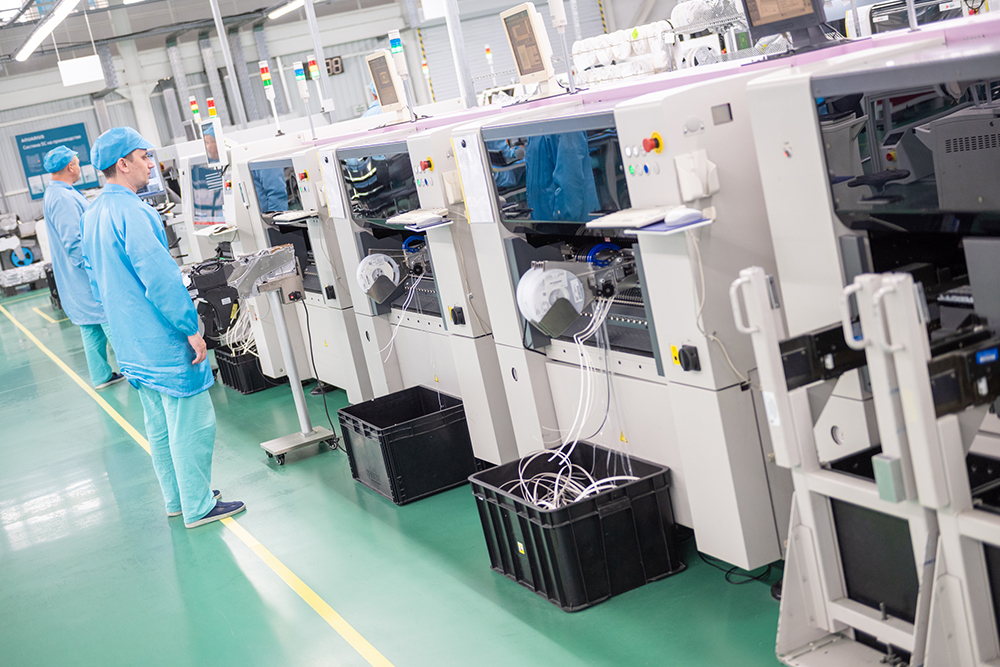
Установка компонентов и оптическая инспекция
Благодаря льготному займу от ФРП на заводе появилась первая в отрасли в России роботизированная линия по установке выводных компонентов. Финансирование подоспело вовремя: «Аквариус» смог получить зарубежное оборудование до того, как цепочки поставок нарушились из-за санкций. «Раньше здесь был конвейер: 30 монтажниц сидели и вручную устанавливали компоненты. Мы достигли пика производства, и установка робота стала оптимальным решением. Людей заняли другой работой, менее монотонной и более интеллектуальной. Семь роботов заменили 30 человек», — рассказывает Реутов.
У каждого робота есть воронка, она напоминает ту часть профессиональных кофемолок, в которую бариста засыпают зерно из мешка. В подобный конус и тоже из мешка на заводе засыпаются компоненты платы. Робот их сортирует и устанавливает, помощь людей ему при этом не нужна.
Одна из задач, по словам Дмитрия Реутова, — минимизировать количество дефектов. Для этого перед тем, как устанавливать компоненты платы, проводят дополнительный промежуточный контроль — оптическую инспекцию. Ею тоже занимается роботизированное оборудование: красный луч методично перемещается по плате под прозрачной крышкой устройства, напоминающего небольшой аппарат МРТ. Робот-инспектор проверяет, что все компоненты установлены правильно.
«Мало кто из наших конкурентов проводит такой промежуточный контроль, — рассказывает Реутов. — Он позволяет скорректировать и работу станков, и весь технологический процесс до того, как начнется пайка. Когда плата спаяна, уже поздно вносить изменения. У некоторых наших коллег сидит по 300 монтажников, которые вручную ремонтируют брак. Мы с нашим объемом не можем себе такое позволить: завод выпускает до миллиона разных изделий в год».
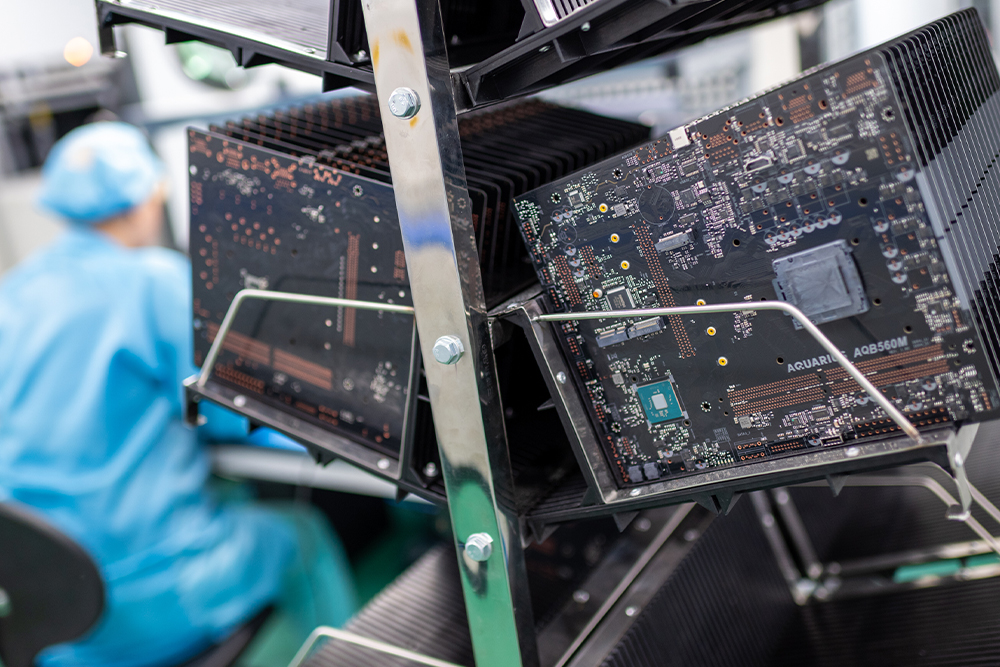
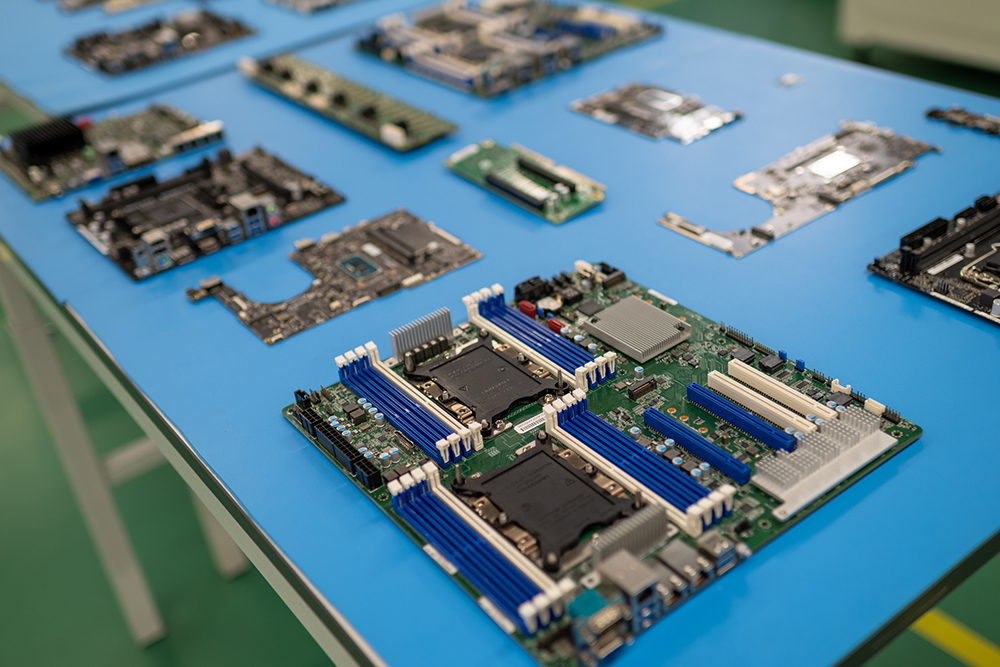
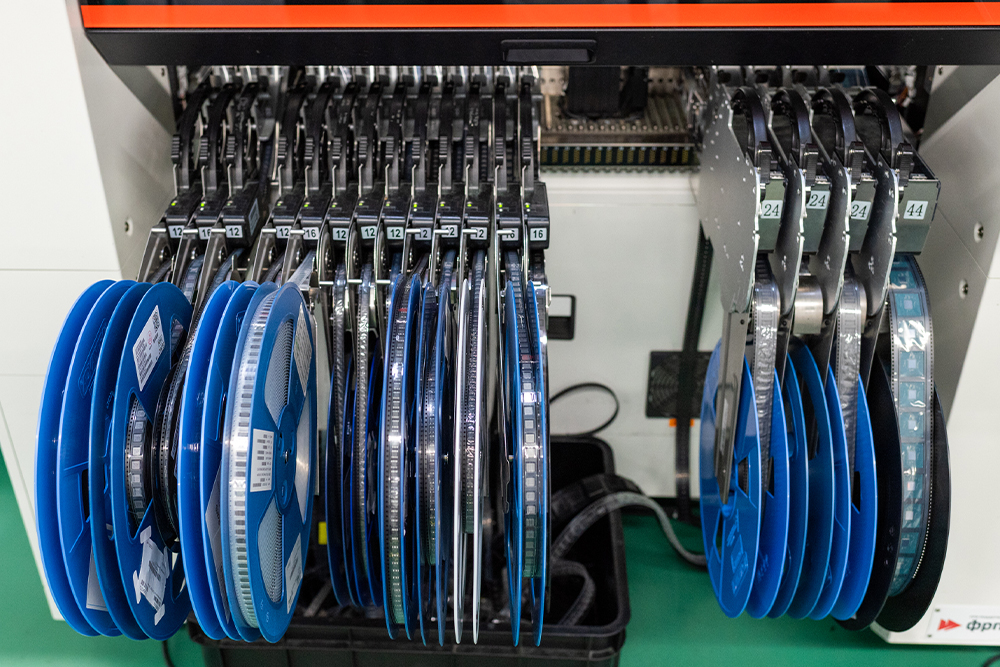