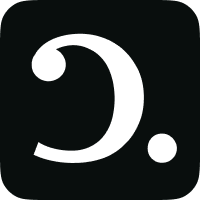
Роботы и люди. Как производят материнские платы на заводе в Шуе
С 1990 года завод группы компаний «Аквариус» в Шуе под Иваново выпускает компьютеры и серверы, позднее здесь стали собирать ноутбуки и планшеты. В 2018 году начали изготавливать и материнские платы, а в 2023-м запустили новую линию по их производству. Посмотреть, как она устроена, отправилась корреспондент «Сноба»
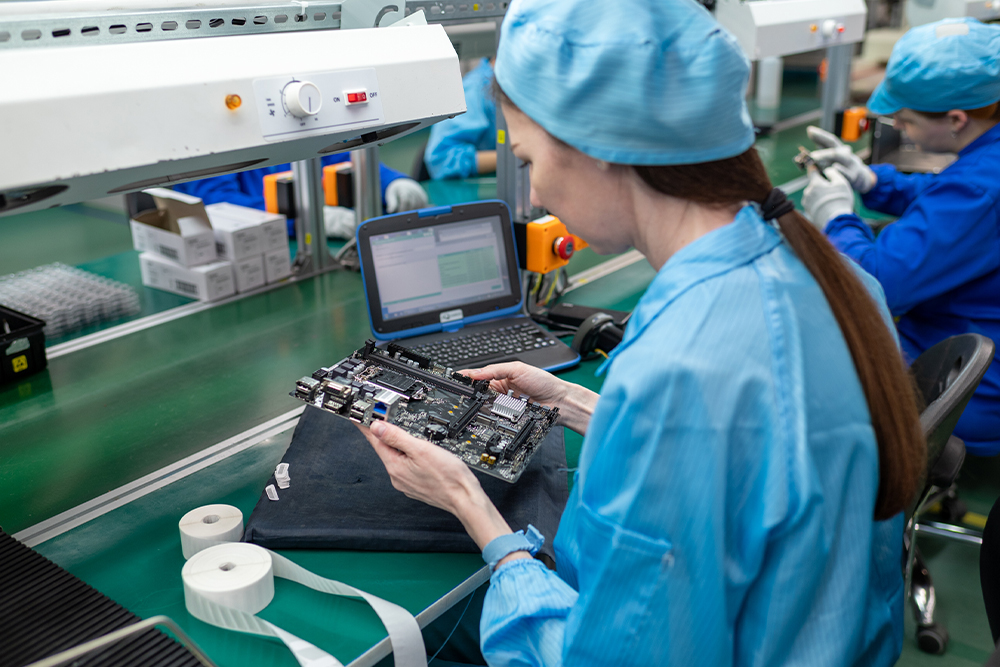
Комплектация и нанесение паяльной пасты
Просторные цеха с высокими потолками и большими окнами скорее напоминают медицинскую лабораторию, чем завод: чисто, светло, аккуратно. Сотрудники одеты в синюю и зеленую форму, похожую на одежду медперсонала. Многие работают в специальных шапочках и перчатках.
Первый цех — комплектация. У каждой детали материнской платы есть свой QR-код. По нему в случае дефектов или поломок можно проследить, из какой партии и от какого поставщика поступила деталь, а также кто и когда работал с ней уже на заводе.
В отделе монтажа печатных плат на пластинки зеленого цвета — «фундаменты» будущих материнских плат — наносят паяльную пасту. Эту технологическую операцию выполняет специальное оборудование: распределяет пасту при помощи трафарета, определяет силу прижатия и скорость движения. «Для каждой платы это индивидуальные параметры, и они на 90% определяют качество дальнейшей сборки изделия», — поясняет Дмитрий Реутов, глава производственно-технологической дирекции «Аквариуса».
Система решает, соответствует ли результат нанесения пасты заданным параметрам и требуется ли корректировка. Изображение образца, на который ориентируется робот, выводится на монитор, установленный над станком, — с его помощью сотрудники завода дают команды роботу.
Сейчас на заводе есть две линии, на которых наносят паяльную пасту. Первую «Аквариус» купил раньше на собственные средства, вторую — на заем, полученный от Фонда развития промышленности (ФРП), что позволило увеличить производительность завода почти вдвое.
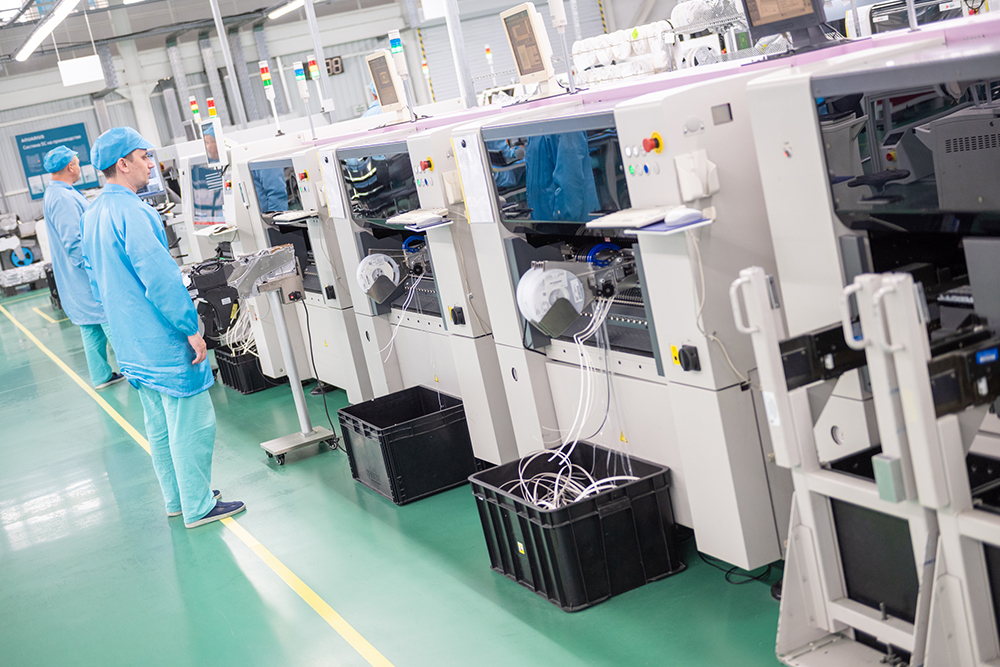
Установка компонентов и оптическая инспекция
Благодаря льготному займу от ФРП на заводе появилась первая в отрасли в России роботизированная линия по установке выводных компонентов. Финансирование подоспело вовремя: «Аквариус» смог получить зарубежное оборудование до того, как цепочки поставок нарушились из-за санкций. «Раньше здесь был конвейер: 30 монтажниц сидели и вручную устанавливали компоненты. Мы достигли пика производства, и установка робота стала оптимальным решением. Людей заняли другой работой, менее монотонной и более интеллектуальной. Семь роботов заменили 30 человек», — рассказывает Реутов.
У каждого робота есть воронка, она напоминает ту часть профессиональных кофемолок, в которую бариста засыпают зерно из мешка. В подобный конус и тоже из мешка на заводе засыпаются компоненты платы. Робот их сортирует и устанавливает, помощь людей ему при этом не нужна.
Одна из задач, по словам Дмитрия Реутова, — минимизировать количество дефектов. Для этого перед тем, как устанавливать компоненты платы, проводят дополнительный промежуточный контроль — оптическую инспекцию. Ею тоже занимается роботизированное оборудование: красный луч методично перемещается по плате под прозрачной крышкой устройства, напоминающего небольшой аппарат МРТ. Робот-инспектор проверяет, что все компоненты установлены правильно.
«Мало кто из наших конкурентов проводит такой промежуточный контроль, — рассказывает Реутов. — Он позволяет скорректировать и работу станков, и весь технологический процесс до того, как начнется пайка. Когда плата спаяна, уже поздно вносить изменения. У некоторых наших коллег сидит по 300 монтажников, которые вручную ремонтируют брак. Мы с нашим объемом не можем себе такое позволить: завод выпускает до миллиона разных изделий в год».
Пайка и тестирование
После проверки оборудование устанавливает на готовую плату компоненты, заранее подобранные под каждое устройство еще на этапе комплектации. Платы переезжают по конвейеру дальше — в печь. Их паяют в среде инертного газа: так можно добиться смычки без пор, из-за которых при использовании гаджета плата может дать трещину. Под печью проложены трассы, которые подают внутрь азот. «Это позволяет при пайке очень нежных компонентов, которые используются, например, при производстве планшетов, обеспечить максимальное качество соединений», — объясняет Реутов.
Когда плата спаяна, она попадает на вторую оптическую инспекцию, где робот оценивает качество припоя и передает человеку информацию о том, на какие места обратить внимание. Оператор решает, нужно ли что-то исправить, машина фиксирует и запоминает его решения и с каждой новой итерацией учится и становится умнее. В будущем это позволит полностью автоматизировать этот этап производства. «Искусственный интеллект несовершенен, он должен проверить действие более 10 тысяч раз, чтобы чему-то научиться, и оператор ему в этом помогает», — рассказывает Реутов.
Готовые платы попадают на конвейер тестирования. Для каждого вида плат есть свои установки, разработанные инженерами «Аквариуса». Задача тестов — проверить каждую деталь платы, чтобы убедиться в ее способности справиться с любыми возможными задачами и нагрузками.
«Так как наши ребята проектируют все сами, они прекрасно понимают, как платы построены изнутри, могут написать технологический БИОС (программа, которая запускается при включении устройства, управляет им, тестирует и активирует все компоненты, после чего передает контроль операционной системе. — Прим. ред.) и, соответственно, нагрузить любой узел устройства до предела возможностей», — рассказывает Реутов.
Те изделия, которые не прошли тестирование, отправляются на диагностику к инженерам — они пишут микропрограммы для проверки конкретного куска платы, не справившегося с тестом. После этого деталь можно починить, протестировать повторно и, в случае успеха, отправить на последний конвейер — упаковочный.
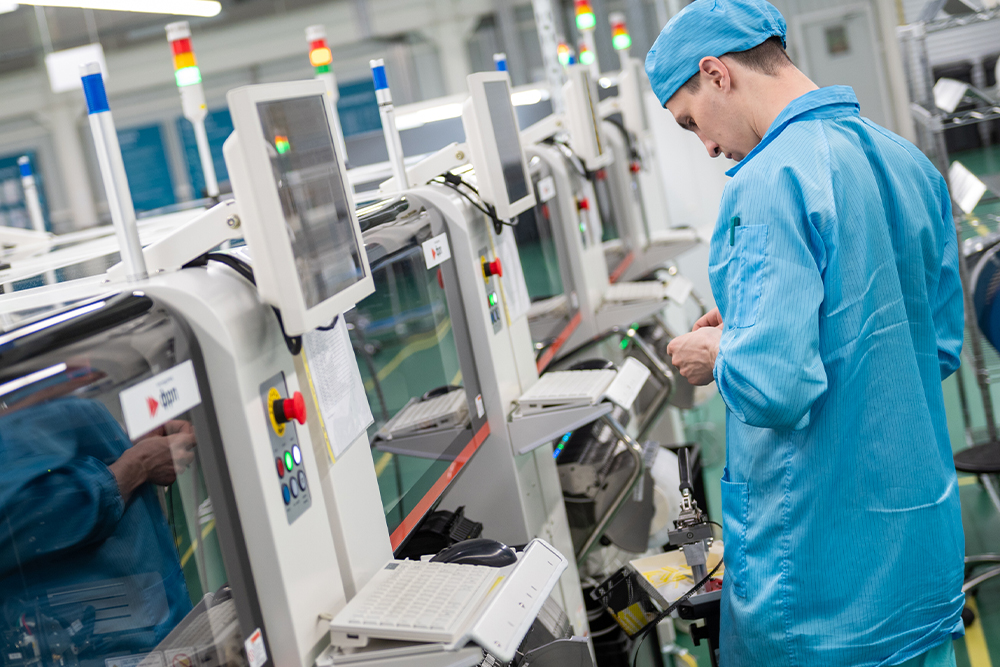
Локализация
Пока российские материнские платы состоят во многом из иностранных компонентов: процессоры, оперативную память, видеокарты, сами печатные платы и другие высокотехнологичные детали покупают, как правило, за рубежом. «Мы нацелены на то, чтобы максимально локализовать все комплектующие, — говорит Дмитрий Реутов. — В прошлом году наладили производство корпусных деталей, теперь все железки выпускают наши партнеры на территории России. Сейчас работаем над переходом на отечественные блоки питания, кабельную продукцию и комплектующие для вай-фай-модулей».
Одна из самых сложных задач — производство процессоров. В 2022 году завод в Шуе выпустил 15 тысяч мини-компьютеров с платами на российских процессорах «Байкал» (разработка компании «Байкал электроникс»). «Это наша гордость, — Реутов указывает на образец платы с “Байкалом”. — Здесь процессор расположен под углом. Мы сделали это, чтобы сократить количество слоев в печатной плате. Мы владеем всеми компетенциями в разработке изделий и можем себе позволить вот такие небольшие фокусы, которые упрощают нам производство, повышают производительность за счет индивидуальной подгонки деталей друг под друга и немного удешевляют продукцию».
«Аквариус» разрабатывает свой процессор. По словам Дмитрия Реутова, вывод устройства на рынок ожидается после 2027 года: «Высокотехнологичные компоненты в России — это вопрос химической промышленности. Я знаю, что очень много отечественных компаний сейчас над этим работают, и ”Аквариус” тоже разрабатывает свои чипы. Это долгий технологический цикл, но главное, что начало положено».
Подготовила Евгения Соколовская